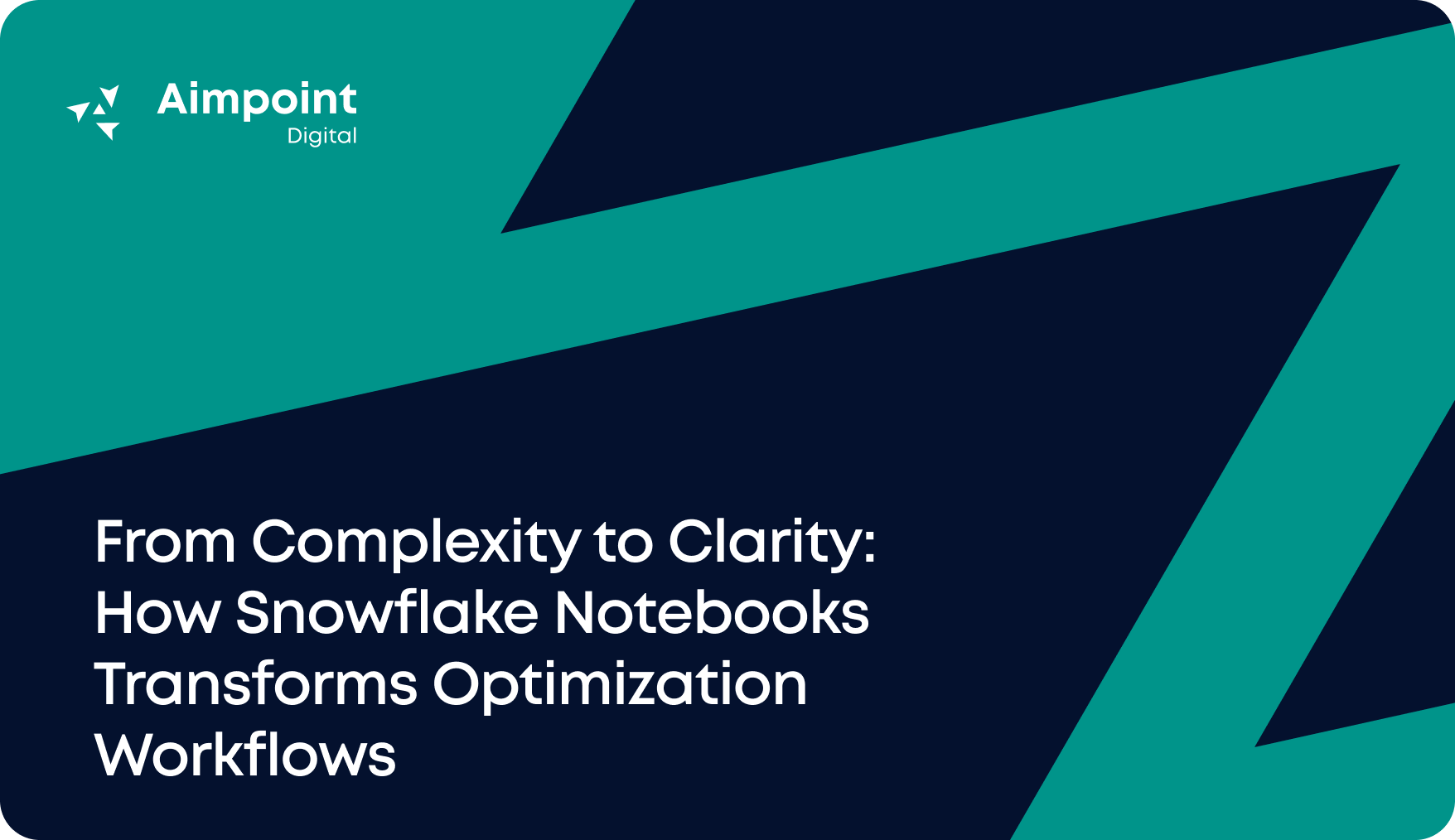
Optimization & Simulation
Plant productivity is about manufacturing quality products efficiently to maximize the throughput of the facility. Whether the plant makes intermediary products or finished goods, the push is often to meet consumer demand. If a manufacturer cannot meet demand, they will fail to capture revenue which may go directly to competitors. Fortunately, there are a variety of methods from data analytics one can leverage to increase plant productivity. Such methods include dashboards, machine learning, statistics, optimization, and simulation. Using data analytics to increase plant productivity either maximizes revenue or improves quality by exploiting data to inform business decisions.
Plant productivity is the output a plant can generate in some window of time. The more output generated, the higher the productivity is. Naturally, the increase in the productiveness of the plant directly affects revenue. Unplanned downtime, or idle machines, is estimated to cost industrial manufacturers 50 billion USD each year. Thus, poor machine allocation, or inefficient use of machines, also directly impacts throughput, and therefore, revenue.
Increasing productivity through analytics requires a sound strategy based on situational analysis of the plant. Gather and validate data, test theories, implement solutions, and monitor changes over time to reap the benefits of plant data analytics.
Minimize risk of inventory shortage or raw material shortage with interactive dashboards:
Minimize delays in production related to late supplier shipments via Machine Learning:
Plan for possible machine failure:
Increase throughput effectively with optimized schedules:
Identify Bottlenecks and Simulate “What-If” Scenarios:
The Aimpoint Digital team has worked extensively with manufacturers using data analytics to increase their plant productivity. Most recently, for a large US manufacturing client, our team utilized advanced techniques to increase throughput to assist the manufacturer in meeting consumer demand. The high number of machine instances and hundreds of product lines created a complex problem to solve. We set up a discrete event simulation tracking each machine instance and product line combination to explore various “What-If” scenarios. Our solution also prescribed optimal strategies for the manufacturer, which resulted in the machine learning solution generating explanatory insights of variables affecting processing times tailored to each machine. Overall, our solution improved the client’s initial baseline model by 25%, generating millions in revenue.
The Aimpoint Digital Team has a proven track record of using cutting-edge tools from data analytics, including dashboards, machine learning, statistics, optimization, and simulation to maximize plant productivity and exceed expectations.
Contact us to increase your plant’s productivity.
Whether you need advanced AI solutions, strategic data expertise, or tailored insights, our team is here to help.