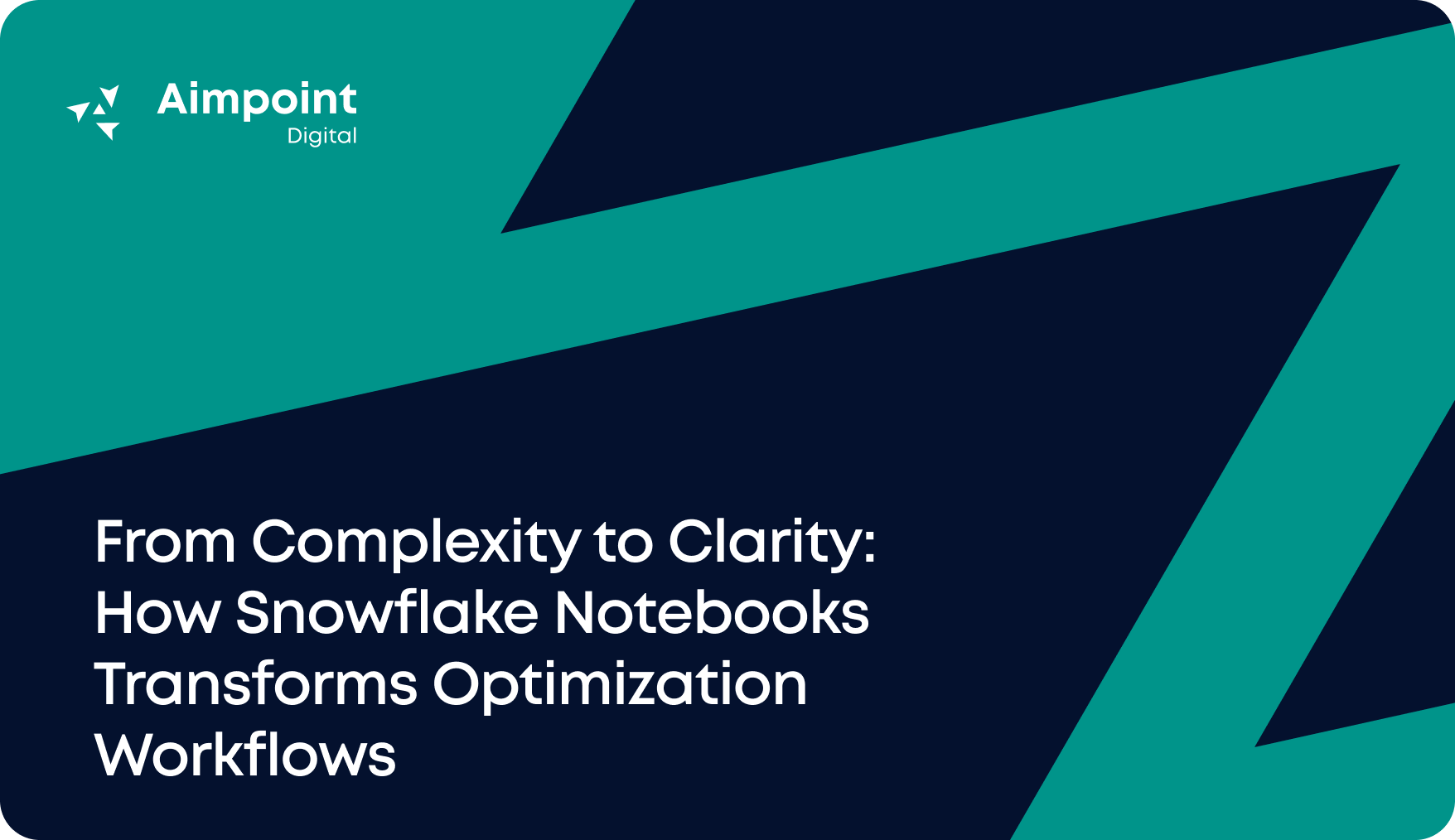
Optimization & Simulation
Typical inventory management policies include a safety stock and reorder point for raw materials and finished products. Optimization techniques can be leveraged to determine the optimal threshold for both values. The typical tradeoffs for minimizing overall inventory costs center around balancing the cost of capital and storage costs for your inventory with the cost of a “missed opportunity” from not having a product available to sell to an end customer.
reduce total working capital investment by 20 - 40 %
For raw materials, optimal inventory safety stock and reordering levels are a function of production plans and scheduling, which in turn are typically a function of customer demand. Additionally, raw material lead times (and their variability) are typically factored into reorder point calculations. The longer the lead time, the higher the threshold will be set for the inventory reordering point to maintain comfortable inventory levels. The shorter the lead time will allow more flexibility in inventory levels and as such a lower reordering point can be set. Given the variability in demand and lead times, stochastic (or randomness) optimization techniques are typically leveraged in calculating the optimal safety stocks and reorder points. The most important parts of ensuring a well-formulated raw materials optimization model include accurate demand distributions, lead time distributions, cost of capital calculations, raw materials storage costs, and missed opportunity costs.
cut down inventory carrying costs by 25 - 45 %
The finished product side of inventory optimization is similar to raw materials optimization with added complexities: production schedule, lead times, and variances. The ability to have finished products is dependent on raw materials. With the potential to not have the right raw materials in the right place at the right time, it becomes probable that finished products will not be produced on time.
Optimization techniques are central to minimizing outbound transportation and logistics cost while continuing to maintain required customer on-time in-full (OTIF) metrics. By pulling in disparate data sources such as finished good inventory levels, production schedules, open customer orders, transportation availability / telematics location (IE where are my trucks / railcars / vessels), and transportation Origin – Destination rate costs, chemicals manufacturers can ensure they are leveraging optimal transportation methods. Typically, outbound logistics optimization techniques leverage single or multi-objective deterministic models to make specific decisions around what transportation modes should be used at what time for which customers.
increase service quality by 30 - 50 %
Manufacturing and distribution networks can be optimized through network optimization and center-of-gravity models. These types of models enable chemical manufacturers and distributors to map out their current supply chain footprint in addition to customer locations. By leveraging optimization techniques, we can determine the optimal locations to reduce transportation and handling costs, decrease time to serve customers, and be better prepared for unexpected event, such as COVID-19. Center-of-gravity models show ideal locations based on a technique call density-based clustering. By leveraging data inputs such as material source locations, customer locations, customer demand, cost breakdowns, business priorities, transportation routing, and prospective customers / facilities, chemical manufacturers / distributors can create business-centric “centers-of-gravity” to drive optimal behaviors across the supply chain network.
lower cost-to-deliver by 25 - 45 %
Aimpoint Digital will help you take an idea from thought through execution. This collaborative journey will enable you to get the most out of your data and technology investments. Contact us to begin your acceleration process.
Whether you need advanced AI solutions, strategic data expertise, or tailored insights, our team is here to help.