Supply Chain Logistics for Agriculture Supply Chain
Discover how we revolutionized multi-stage production and logistics planning with a Python-based MIP model, reducing schedule generation from two weeks to minutes and significantly cutting costs.
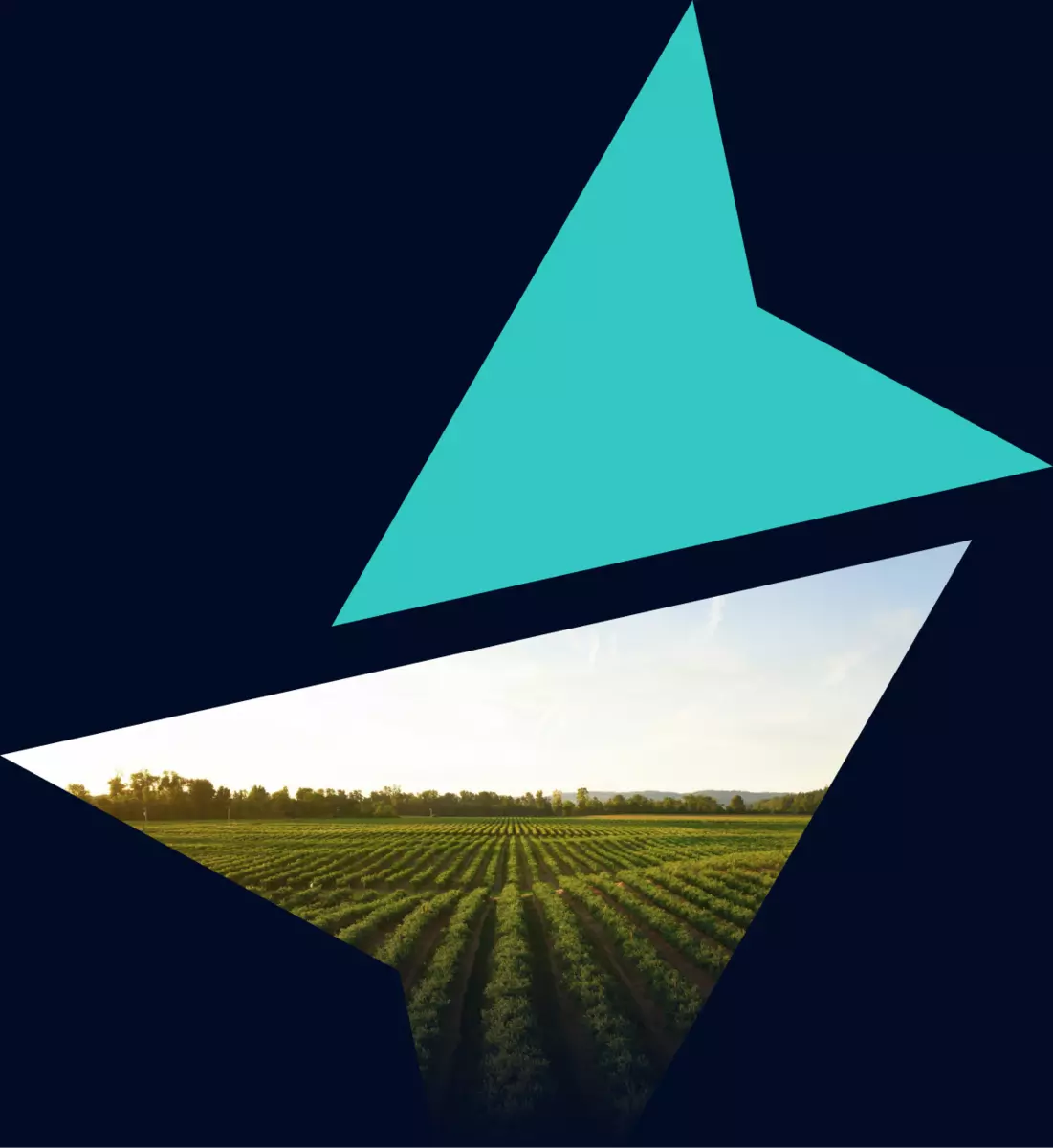
The Challenge
Our client struggled to plan multi-stage production and shipments internationally with the involvement of third-party logistics providers. The existing process took two weeks to generate a schedule and meet customer demand. They needed a more efficient way to plan logistics activities, minimizing cost and time while meeting demand.
Our Approach
We built a solution encompassing the network of international production, treatment, preparation, and distribution facilities. We constructed a workflow that starts with gathering data directly from the customer’s SAP system and datalake. We then built a MIP (mixed-integer programming) optimization model using Python/PuLP to generate a cost-reduced schedule to meet customer demand while respecting supply chain constraints, including location-location movement restrictions (e.g., tariffs & embargos), pre-processing limitations, and subproduct storage time limits.
Results
The new schedule provided a solution in minutes, replacing a manual system that took up to two weeks.
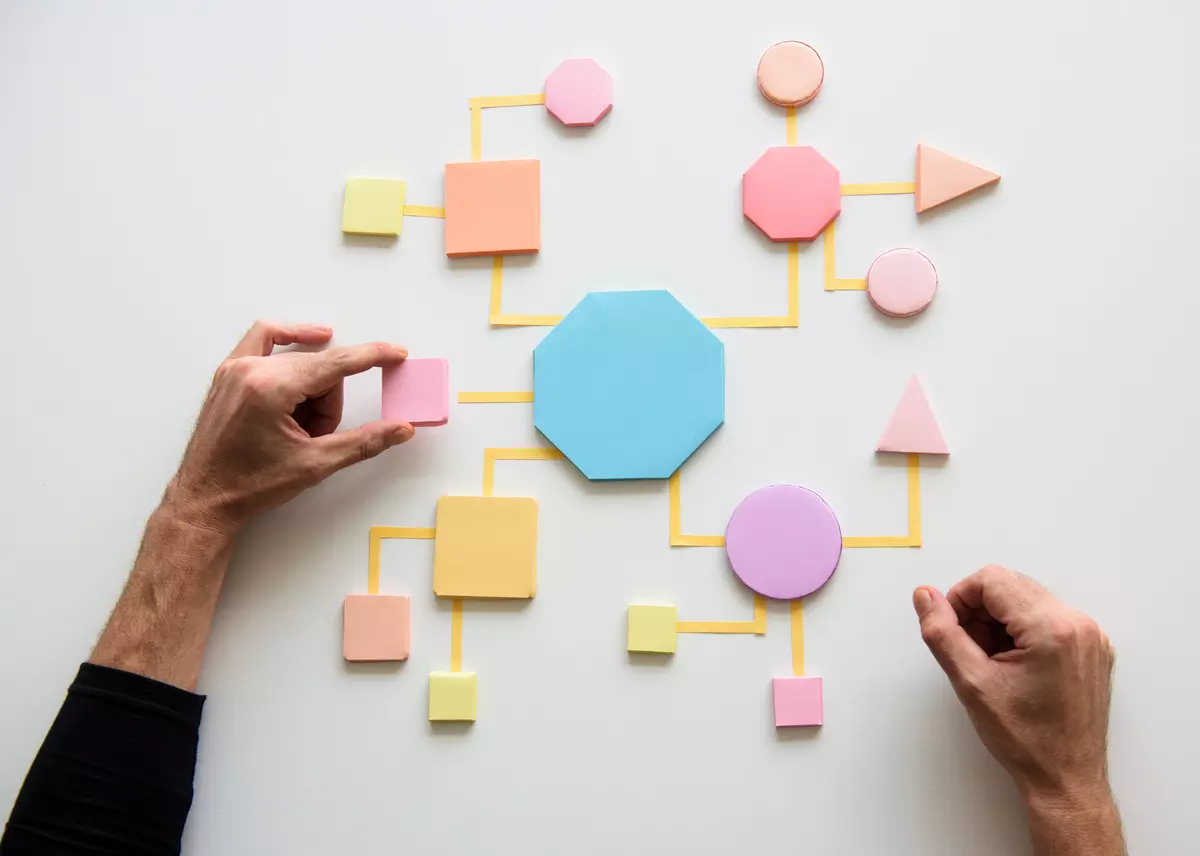
The new schedules could save millions of dollars with efficient network utilization.
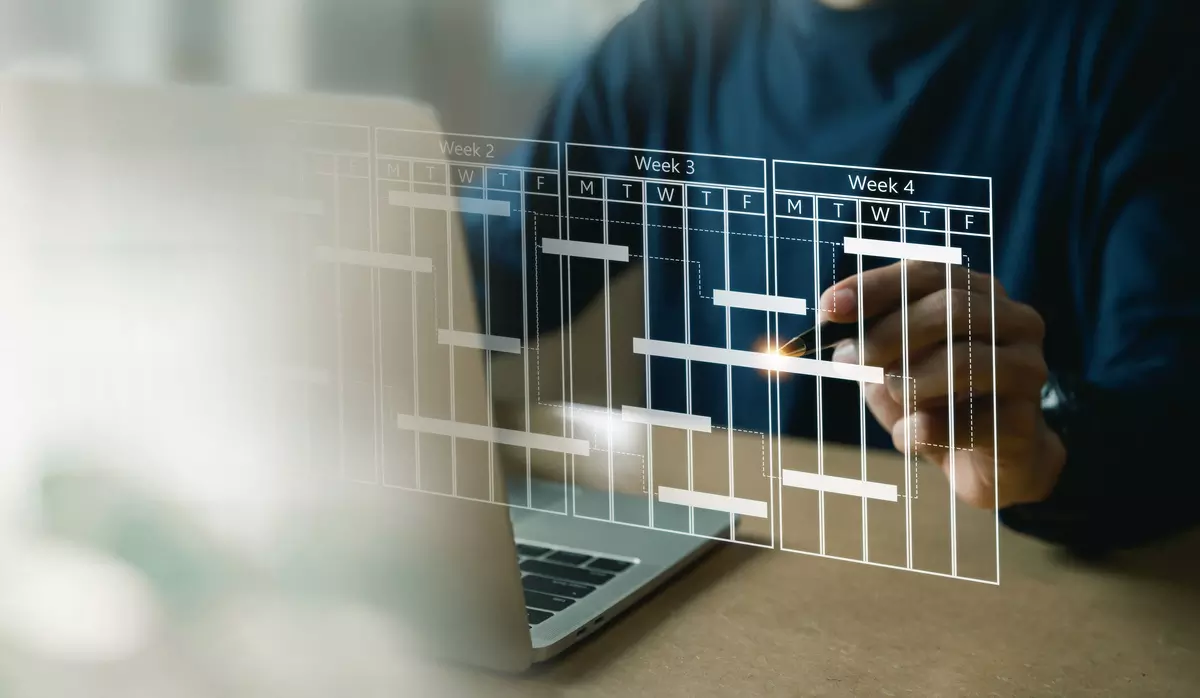
Easily testing future scenarios, like tariff changes or route shutdowns, is now possible.
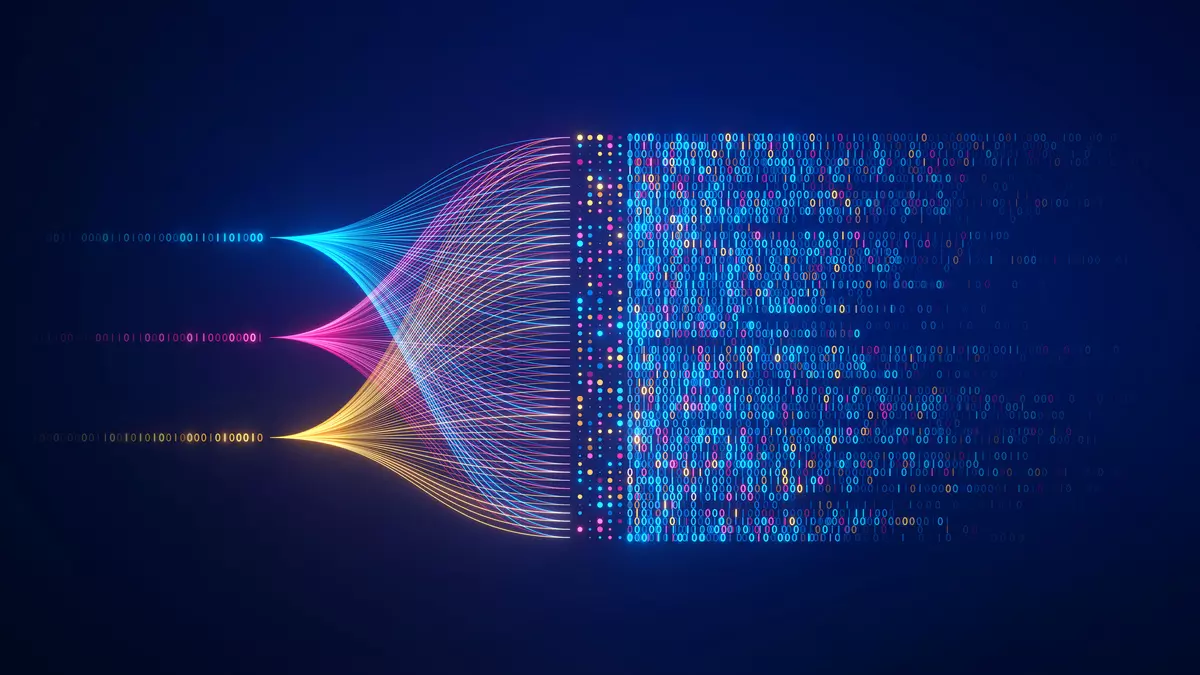
Key Takeaways
Improved decision making doesn’t just save time; it leads to cost reduction across the board, from logistics to overall business operations.
Expected Takeaways
Related case studies
Let’s talk data.
We’ll bring the solutions.
Whether you need advanced AI solutions, strategic data expertise, or tailored insights, our team is here to help.