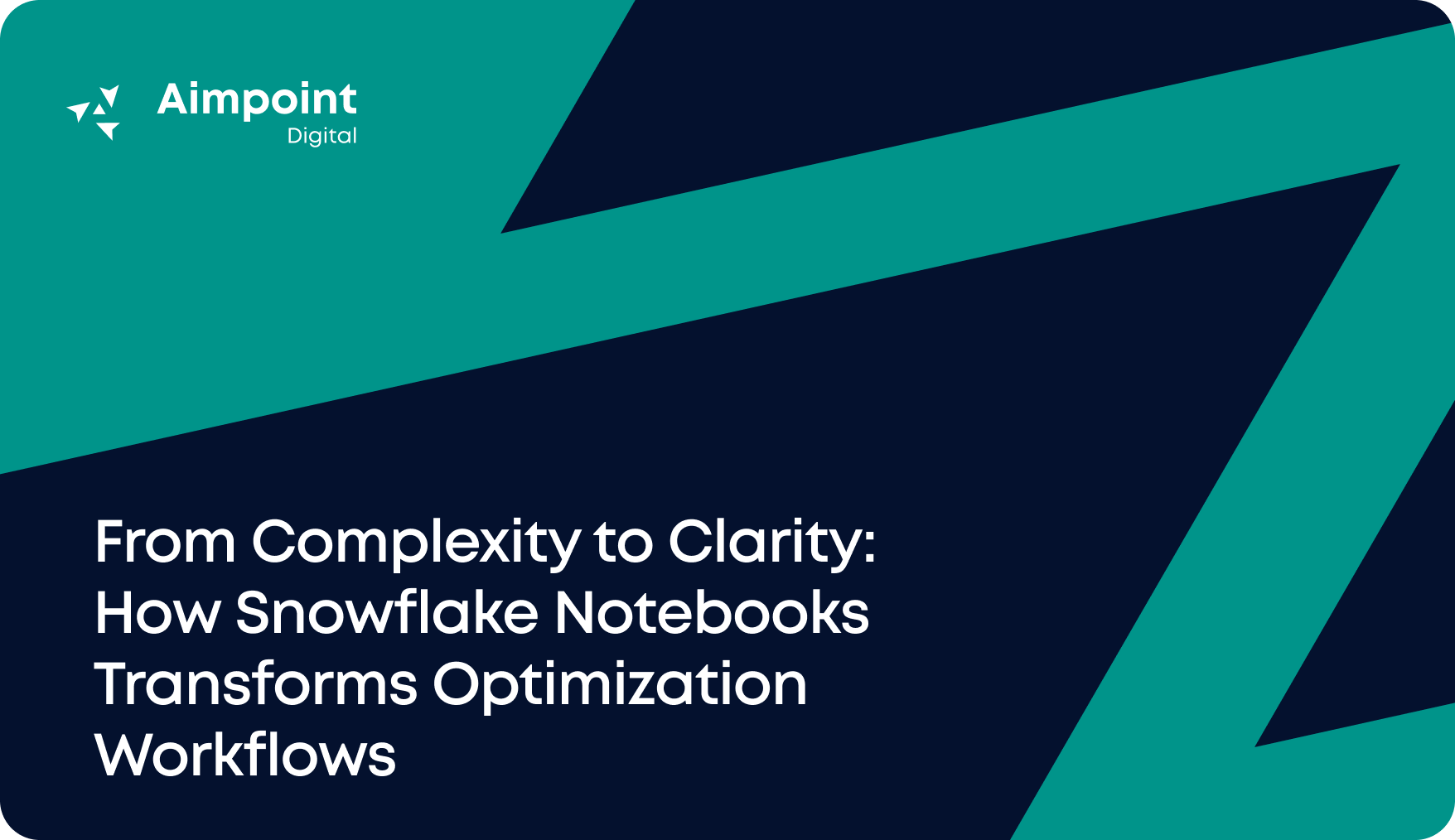
Optimization & Simulation
Efficiently operating available equipment is essential for manufacturing companies in competitive markets. With the proliferation of data in modern enterprises, various approaches to generating production schedules have emerged. The impact of having good scheduling solutions extends beyond maximizing throughput. For example, the ability to evaluate multiple scheduling scenarios effectively assists long-term financial planning and investment decisions for capacity expansion.
Aimpoint Digital’s scheduling solution enabled our pharmaceutical client to generate optimal production schedules in under 40 minutes (reduced from 2 weeks with the client’s initial processes) and allowed increased throughput of millions of dollars.
Our client utilized manual processes employing heuristics for generating production schedules. The client required production schedules for a horizon of over two years with over one hundred demand batches. The scale meant that the heuristic processes took weeks and often led to suboptimal solutions.
The challenge of generating production schedules is evaluating and identifying the best possible schedule given all operating constraints. We implemented a continuous-time batch scheduling model using mixed integer linear programming (MILP). MILP-based optimization models allow us to explore the search space of all production schedules efficiently. Furthermore, MILP models are flexible and can easily incorporate many operating requirements, including the following:
At Aimpoint Digital, we follow an iterative development process with continuous and extensive testing. We developed multiple versions of our optimization model and obtained continuous feedback from our stakeholders on the validity of the model solutions. This process helped us ensure that all modeling assumptions were transparently communicated and verified by our stakeholders and that the solutions generated were practical and feasible.
We always emphasize ensuring that the solutions we develop are user-friendly and maintainable long term. We integrated our optimization models within the client’s existing ERP tool to ensure the smooth adoption of the solution in production.
Aimpoint Digital’s solution generated a 2-year optimal schedule that could fulfill all demands two months ahead of their due dates.
This was significant for our client as they can now produce 10 additional batches to be produced in the same period, amounting to millions of dollars in increased throughput. The model generated the schedule in less than 40 minutes. The dramatic reduction in the time to generate schedules provided the planning time with a new-found ability to evaluate alternative solutions and re-optimize schedules as needed if product demands changed.
Optimization models can provide such massive benefits because of their ability to effectively explore the feasible space and come up with solutions that can be counterintuitive. As an example, suppose we have the following demand batches:
A commonly employed heuristic to generate a feasible schedule is prioritizing batches for production due earlier. For the above demand, this would imply first producing the two batches of Ketoprofen, followed by three batches of Naproxen and three batches of Ibuprofen. This instinctively appealing approach also minimizes the number of changeover operations (i.e., resource idle time). However, this strategy will only sometimes lead to the smallest makespan. The figure below compares the optimal schedule against the result of the rule-based approach.
Left: Heuristic schedule created based on the order of the due dates and products. Right: Optimized schedule with makespan minimized (click to expand).
Note: To avoid disclosing proprietary data, the visualization shown in the Tableau dashboards is illustrative and anonymized.
By separating the Ibuprofen batches, the optimized schedule led to 35-hour time-savings. In practice, our client found an increased number of changeovers were often worth the time saved and the extra throughput in batches generated as a result. This example underscores the advantage of optimization; it helps you identify solutions you may not have thought of in the first place.
Our optimization experts are ready to help you with your production scheduling needs. Contact us through the form below to learn more about creating automated solutions to generate efficient production schedules for your operations.
Whether you need advanced AI solutions, strategic data expertise, or tailored insights, our team is here to help.